2、基本技术要求
建立线棒分厂生产过程计算机群控系统,用一台计算机(上位机)实现全分厂热处理炉生产过程计算机监控,基本技术要求如下:
2.1、 集中显示炉温、运行时间等工艺参数。
2.2、具有工艺编辑及储存功能。
2.3、具有报警及记录功能:记录报警时间、报警值、炉号并存储以备查询。
2.4、 显示历史数据曲线
: 历史记录的追忆查询,历史记录可存储3年或更长。
2.5、 生产技术管理功能
:根据用户要求编制打印生产报表。
2.6、 系统可与集团公司网络通讯,有关职能部门经授权可查看分厂生产情况。
二、设计方案
1、设计原则
本方案依据中钢集团邢台机械轧辊(集团)股份公司工装部和线棒分厂提供的热处理炉有关技术资料和对控制系统的基本技术要求,并针对线棒分厂热处理生产工艺特点及电炉控制柜分布情况制订。在充分保证系统可靠性的前提下,本着技术先进、质量可靠、便于维护、节约成本的原则,最大限度地追求系统的性价比,以确保投资者利益。
1.1 在系统先进性方面:系统结构模式、工艺参数控制调节方式及系统的基本性能,保持与国内外先进技术同步。
1.2 在系统可靠性方面:设备选型所采用设备或仪表均是我们长期使用、实践证明是质量可靠的产品,即主要设备或器件采用进口品牌,辅助器件选用国内知名品牌。
1.3 可维护性方面:所选用的设备、仪表及其备件,均在国内市场有经销商和技术服务机构,能够方便地采购备品备件和提供技术支持。
1.4 节约成本方面:线棒分厂原来的控制设备、仪表、电器、计算机在不影响上述设计原则的前提下尽量选用,节约投资成本。
2、系统概述
该系统采用上、下位机、智能仪表三级监控,配一台上位机带
2台下位机。一台下位机分别带4台热处理炉,即1#-4#炉配一台下位机,5#-8#炉配一台下位机,组成分布式网络监控系统。
2.1 上位机采用工业控制计算机,集中显示各台电炉炉温、运行时间等工艺参数集;编辑生产工艺;以曲线、数据两种方式记录查询历史数据;
报警点记录、生产报表打印及工件档案管理等功能.
2.2 电炉智能控制柜,用进口原装智能PID程序调节器(带通讯口),主要负责电炉温度等信号的采集与控制,并将数据通过通讯接口上传至工控机系统。
2.3 正常情况下,控制柜完全接受工控机系统的指令对电炉炉温进行控制;特殊情况下,控制柜脱离上、下位机,直接对电炉炉温进行控制,各段的温度、时间等参数可通过仪表面板按键进行设定。
3、系统结构框图
图例说明:

:屏蔽电缆

:工业计算机

:局域网线
三、系统基本性能
1、上位机基本性能
1.1 主控界面:
集中显示炉温、运行时间;并支持炉温、运行时间设定值在线修改。
电炉加热开启、暂停、工艺结束手动、自动控制功能。
工件出炉前(如10分钟)及工艺结束报警提示功能。
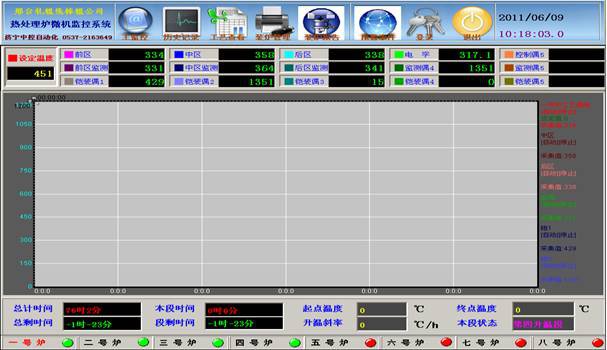
1.2 工艺编辑储存:
进行工艺编辑,并将常用工件的生产工艺储存到存储器,使用时直接调用。
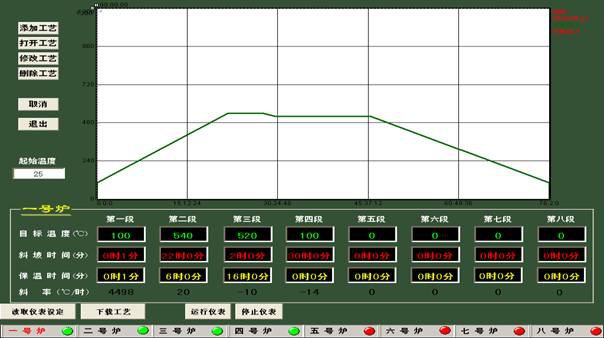
1.3 报警记录:记录报警时间、报警值、炉号、区号并存储以备查询。

1.4 实时及历史数据曲线
:
以数据表和曲线两种方式显示实时和历史记录,并支持历史记录的追忆查询,历史记录可存储3年或更长。曲线纵、横坐标显示范围可调,适用于多种炉温范围显示。
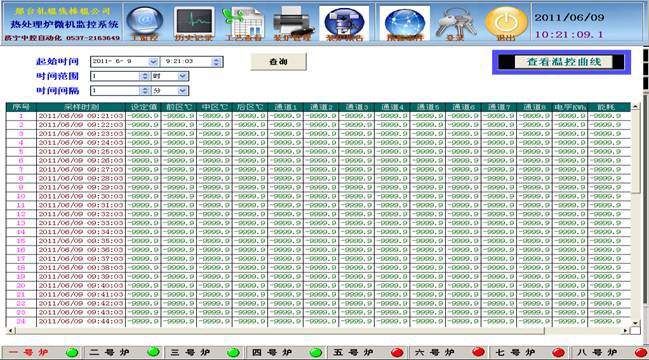
1.5 生产管理
:
根据用户要求编制生产报表,并具有手动打印和定时自动打印功能。
每批产品的编号、工件名称、图号、装炉时间、出炉时间、保温时间、加热温度、数量、炉号、操作工姓名等自动存档,形成各批工件技术档案。
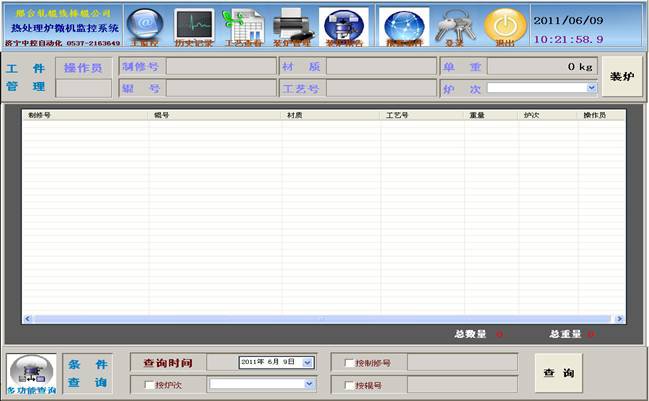
1.6 授权限制:
被授权人员(如工艺工程师)输入密码后,可对重要工艺数据或控制参数进行修改。一般操作工不能进行该操作。

1.7 功率平衡表:
显示每台炉每个区当前输出功率、总输出功率,并有报警功能。
2、下位机基本性能
2.1 负责对现场控制柜各智能仪表的数据信息进行集中采集和存储。
2.2将采集的数据经局域网上传至上位机,在上位机上实现设备的监视和群控等操作。
2.3接收上位机发出的工艺操作指令并向现场智能仪表转发,从而实现对智能仪表的远程控制。
3、电炉控制柜主要功能:保持原控制柜基本功能不变。
四、系统基本配置
1、工控机系统基本配置
上位机硬件配置:工业级计算机IPC-610机箱、PIV3.0CPU、512M内存、160G硬盘、19″彩色显示器、DVD光驱、集成10M/100M自适应以太网卡、显卡、操作员键盘、鼠标等。
下位机硬件配置:工业级计算机IPC-610机箱、PIV2.8CPU、512M内存、80G硬盘、DVD光驱、集成10M/100M自适应以太网卡。
软件包括三维力控的PCAUTO5.0组态软件及我公司开发的热处理工艺应用软件。
2、控制柜基本配置
原控制柜基本不动,仅将原控制柜上的智能调节仪按统一型号进行更新,配置485通信接口。该方案主要考虑节约成本,不影响正常生产。